Alodine and anodize are two finishes used on aluminum parts that tend to get confused with one another. In this article, we hope to clear up some of that confusion by describing what each process is, and the advantages and disadvantages of using each. While anodize is generally a more robust finish than alodine, they both have their place. We hope that by understanding more about them, you can better select the best finish for your project.
Before we get started, let’s clear up some terminology. Alodine is technically a trademarked name of a specific chemical. The more general term for the process is chromate conversion or chemical film (chem film for short). Like Kleenex and tissue, Alodine has become synonymous with chem film and gets used interchangeably across most industries. So if you see any of those terms, just know they all refer to the same thing. We’ll use them all throughout this article.
Anodizing is available as one of the multiple finishing options for aluminum parts from SendCutSend.
Alodining vs. Anodizing: How Does Alodining Work Exactly?
Since anodizing is a process offered by SendCutSend, we’ve covered it in detail in its own article. We’ll cover a little more of how the alodining process on aluminum works.
Alodine differs from anodizing in that it is a chemical film rather than an electrochemical process. There’s no electrical current involved in the alodine process, instead, clean aluminum parts are submerged in a room temperature chemical bath to form a thin protective film of mostly chromium oxide on the surface. The chemical solution could also be sprayed or brushed onto the parts, but submerging is common to more easily and quickly cover the entire part. It only takes a few minutes for the layer to form, then the parts are rinsed and allowed to dry. Initially, the film is very soft, but as it dries it gets harder and stronger. Although it never reaches the strength of anodizing.
Anodizing, on the other hand, uses the aluminum as the anode (hence the name) in an electrochemical acid bath process to form a thin, hard layer (but thicker than the layer that forms naturally on aluminum) of aluminum oxide.
For both alodining and anodizing, the part needs to be extremely clean. The parts are thoroughly degreased and sometimes even acid etched in the case of anodizing.
Neither process leaves an opaque coating like paint or powder coat. Any imperfections in the material surface will show through and may even be highlighted afterwards. So if the best possible appearance is important, you’ll want to get the desired uniform look/texture on the surface before starting either finishing process. Brushed finishes and blasted finishes to different levels are popular methods for achieving that uniform look.
Applications of Alodine Coating
So why would you want to use a chem film on aluminum? Similarly to anodizing, its purpose is to passivate (to make non-reactive) the surface to prevent further oxidation. Let’s explore some of the advantages to alodine and where you might choose to use it.
Low Cost Applications – Chromate conversion is a less expensive process than anodizing. The materials themselves cost less, and because the process is simpler there’s less equipment involved and less labor to use alodine vs anodize. In applications where the cost to finish is a major driver, alodine can be a good choice. Keep in mind that a low cost way to anodize aluminum is by ordering parts through SendCutSend.
Ease of Application – For applications where finishing will be done in-house, alodine is an easier choice. The alodining process is simpler and faster than anodizing. No electricity is involved, just a single chemical bath and quick dunk followed by a rinse. Both chem film and anodize require the parts to be thoroughly cleaned for the best results. For SendCutSend parts, however, anodizing aluminum is as easy as checking the right box during your order.
Thermal and Electrical Applications – In applications where thermal or electrical conductivity are important, alodine is a more appropriate choice. Heat sinks are often chem film coated rather than anodized. Anodized aluminum components that require electrical grounding (or electrical contact of any kind) often need to have surfaces masked since the anodized oxide layer is much more electrically resistive.
Pretreatment for Paint – One of the most common applications of alodine is as an adhesion promoter for other coatings like paint. Professionally painted aluminum surfaces often have a chem film applied prior to paint.
Precision Fit Applications – While anodizing is generally considered to be a relatively thin coating (especially compared to finishes like paint and powder coat), it is still thicker than chem film. This thickness can be beneficial for protection, but can also be problematic when tight fits are required. Alodine is a layer on the surface of the metal with some thickness, but generally it is much thinner than other finishes. Alodine is used often in aerospace applications that require precise fits.
Alodine Finish vs. Anodized Finish: 3 Limitations of Alodine Coatings
Alodine certainly has its place, but it also has its limits, especially compared to anodizing. Let’s look at some of those limitations in more detail.
- Less Durable – A chromate conversion coating on aluminum is not very durable. The layer is thin and relatively soft and can be scratched or damaged very easily. It is typically considered a temporary finish by itself. Alodine is a more common finish for prototype parts or parts used for testing rather than final parts. It isn’t a good choice for parts that may see abrasion or wear. Anodizing aluminum is much better for resisting wear. It has a thicker, harder protective coat that’s integral to the surface of the substrate. Type III anodizing (also called hard coat anodizing) can be used, which produces an even harder, more wear resistant finish than Type II. Both types of anodizing are available from SendCutSend.
- Fewer Colors – Both alodine and anodize can be done in a clear finish, but the only other color option for alodine is a yellow/brown color. Anodize, however, can be dyed nearly any color. SendCutSend currently offers five different colors of anodizing, including black, clear (Type II and III), red, yellow and blue. See the anodizing page for examples of each color.
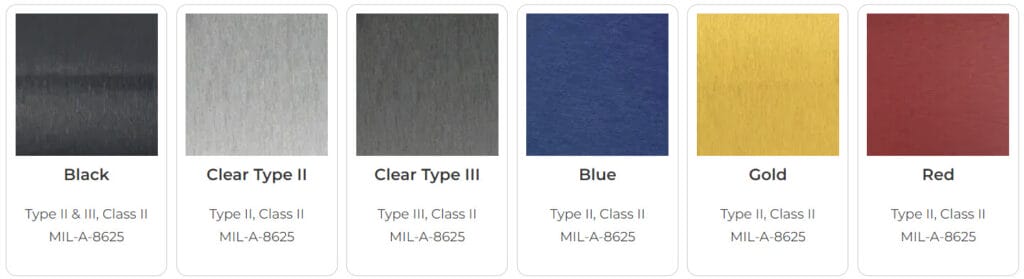
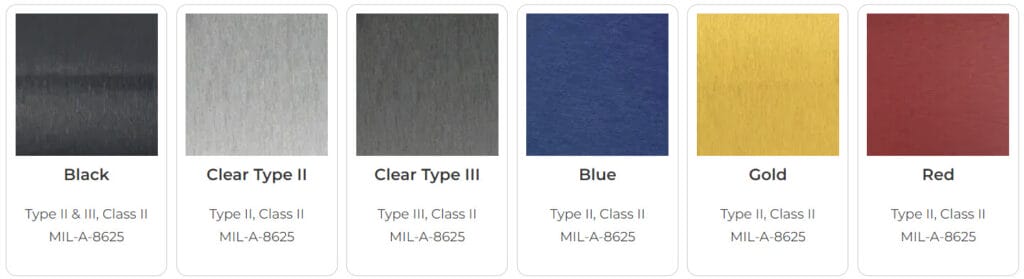
- Less Lubricity – The opposite of adhesion, anodized surfaces are great for lubricity, meaning parts can slide across each other with less friction. Combined with increased durability, anodizing is a much better finish for moving parts and mechanisms. This trait also makes cleaning of anodized surfaces much easier than alodine. Fewer things will stick to an anodized surface.
Industry Uses for Alodine and Anodize
Both alodine and anodize finishes are used across nearly all industries.
Aerospace – Anodize finished parts are used in aircraft and spacecraft because of its long lasting durability and corrosion resistance along with its ability to reduce friction. Alodine is used on less exposed components where precise fits are needed.
Automotive – Aesthetic, durable finishes are needed to manufacture vehicles. Anodizing provides both these traits with ease.
Military/Defense – Both alodine and anodize will reduce the gloss of an aluminum part, something desirable in a lot of military and defense equipment. Anodizing aluminum allows for greater corrosion protection along with the desired appearance without the need for secondary coatings.
Electronics – The ability of anodize to electrically insulate and alodine to retain electrical conductivity makes them useful in electronics applications.
Architectural – Corrosion protection and aesthetics make anodizing aluminum useful in architectural applications where parts have to look good for years while being exposed to the elements.
Marine – There are fewer environments more corrosive than the ocean. Salt water speeds up corrosion so durable finishes are a must. Anodizing is strong enough to be used in these areas.
Should You Choose Anodizing or Alodining?
Which finish is best for your project will depend on a lot of factors. Anodizing offers the best corrosion protection, wear and is the better long term choice in most cases. Alodine has the advantage of electrical and thermal conductivity. For parts that will be painted afterwards, alodine may be a good choice.
You may also want to consider when and where your parts will be finished. If you intend to finish the parts yourself, alodine is the cheaper and easier process, where anodizing will require some extra equipment and knowledge. For short term protection, or as an intermediate finishing step, alodine makes more sense. If you’re ordering finished parts from SendCutSend, you can just check a few boxes during your order and get your aluminum parts anodized in one of a handful of colors we offer. For readers that want to give anodizing aluminum a try on their own, we’ve written an article to help with that too.
Giving Your Parts Longevity and Improved Resistance with Anodizing
For a durable, long term finish on aluminum parts, anodizing beats alodine. It’s only in a few key areas that the chromate conversion process has an advantage over anodizing. When you require better thermal and electrical conductivity, as a low cost temporary protection method or a pretreatment prior to paint and when you need to minimize the impact on the overall dimensions of your parts are alodine’s strengths.
Even though anodizing aluminum is a more complex process, it offers much better protection from oxidation and wear. It’s available in multiple colors and has a slick surface that can be cleaned much easier. Anodizing also has the distinct advantage of being available directly from SendCutSend so you can get a quality finished part quickly and easily.
For more information on anodizing from SendCutSend, check out the services we offer and our blog.
FAQs about Anodizing and Alodining
What is alodining?
Alodining is a chemical film process, also known as chromate conversion. It’s used to passivate the surface to improve corrosion resistance.
Can you alodine and anodize?
Yes. In fact, applications like electrical enclosures that require an electrical ground contact often have a chem film applied to areas where the electrical contact is made and anodized everywhere else. This provides the advantages of both and still provides the desired protection. Alodine can also be used as a simple way to touch up damage to an anodized finish.
Are there different types of alodine and anodize?
Yep. For chromate conversion, see MIL-DTL-5541, which covers Type I (older and more dangerous using hexavalent chromium) and Type II (more current and safer non-hexavalent chromium option) and the different classes. It also covers application methods and test procedures for quality. A must have spec for calling out chem film on a technical document.
For anodizing on aluminum, see MIL-PRF-8625 which similarly covers Types, Classes and procedures.
Can I alodine or anodize over weld seams?
You can, but if you know you’ll be anodizing your parts after welding, you may want to avoid using 4043 filler. Even when the weld seam is ground flush, the anodizing process reacts differently with 4043 filler than the base aluminum and the color will be different. It should be a cosmetic difference only, but if you want everything to look uniform after anodizing, look into using something like 5356 filler instead.
Can materials other than aluminum be anodized or chem filmed?
Yes. We only discussed aluminum here because that’s a very common material for both processes, but both finishing processes can be used on other materials such as titanium and magnesium. Chromate conversions can be done on even more materials. Chromate conversions are used after zinc plating steel parts to better protect the soft zinc.